At Scanflow, we have successfully tackled a critical issue affecting the quality of manufactured parts for one of our industrial clients: the detection of carbon soot particles on conveyor lines. In high-speed manufacturing environments, every detail matters, and foreign particles can lead to considerable quality issues. This technical article will walk through our intelligent solution for detecting and managing carbon soot—a byproduct of industrial heating and cooling processes—leveraging state-of-the-art vision intelligence.
Our client, a high-volume manufacturer of metal items like nuts, bolts, washers, and studs, operates with multiple conveyor lines to streamline the heating, cooling, and processing of these components. However, during these intensive processes, chemicals and materials evaporate and condense, forming solid particles known as carbon soot. As the conveyor transports metal items for further treatment, carbon soot particles often latch onto them, obstructing the heating process required for rigidity. This interference weakens the metal components, compromising their durability and quality, which directly affects the reliability of the finished product.
The project’s primary objective was to develop an intelligent, automated system capable of detecting and alerting operators about the presence of carbon soot on conveyor lines. By achieving a high detection accuracy, we aimed to enhance product quality and reduce rework costs, aligning with our client’s quality control standards. Our solution integrates advanced vision intelligence with high-speed alert and response mechanisms to deliver an effective end-to-end solution, achieving a remarkable 99% detection success rate.
The developed solution is a sophisticated vision intelligence system, combining powerful hardware and advanced AI algorithms. Below are the essential components:
- 1. Hardware Units
- High-Definition Cameras: Strategically placed to capture detailed visuals of conveyor belts, the cameras are capable of continuous, high-speed monitoring.
- GPU-Accelerated Processing Unit: A dedicated GPU server allows the system to process high-resolution images in real-time, facilitating rapid soot detection.
- Fiber Optic Communication Unit: For seamless data transmission, fiber optic technology ensures minimal latency in communication between system components.
- 2. Software
- AI Model for Soot Detection: Our proprietary AI model was trained on client-specific data, using supervised learning techniques to achieve robust performance metrics. With an accuracy rate of 98%, the model leverages state-of-the-art object detection and classification algorithms, performing localization and segmentation for precise carbon soot identification.
- User Interface (UI): The system includes an intuitive UI for real-time monitoring and configuration, allowing operators to customize key settings such as detection thresholds, storage paths, and alert configurations.
Our AI research engineers designed and trained the model using client-specific data collected from the production line. Here’s a summary of the steps involved:
- Data Collection and Annotation:
Visual data was collected from the client’s conveyor systems, followed by extensive annotation to mark carbon soot instances for supervised learning.
- Model Training and Optimization:
Using advanced hyperparameter tuning techniques, the model was trained for 1.5 days in our research lab, leveraging GPUs for accelerated learning.
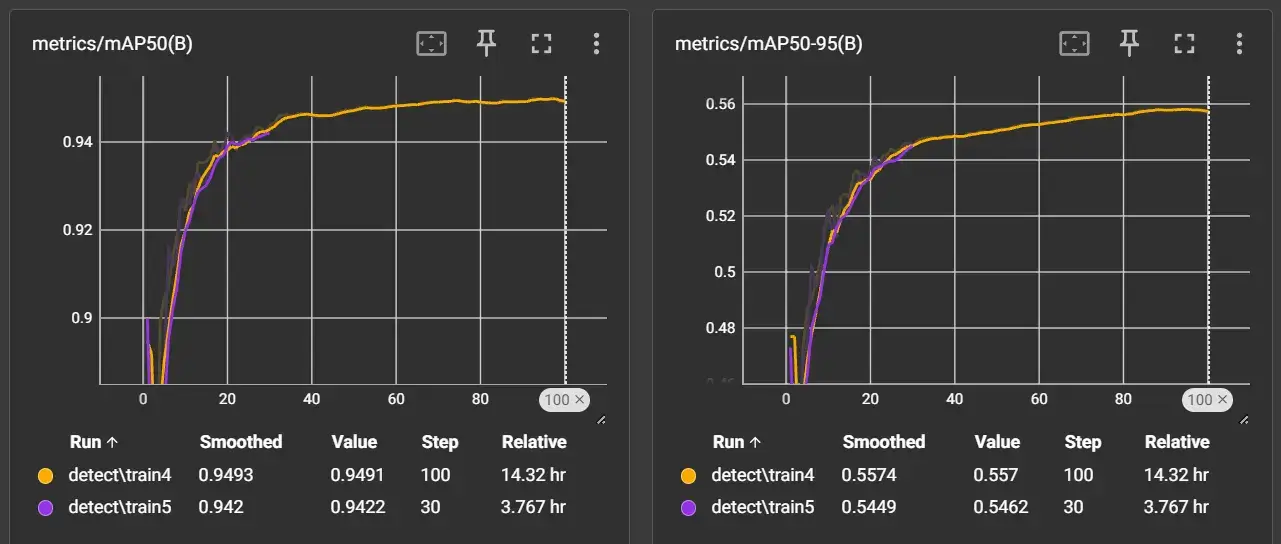
- Model Security and Deployment:
The AI model was encrypted with AES-256 security standards, ensuring data privacy and system integrity in the client’s production environment.
The model underwent extensive evaluation using metrics specific to object detection, classification, and segmentation. Final deployment followed successful on-site testing, verifying the model’s high accuracy and consistency.
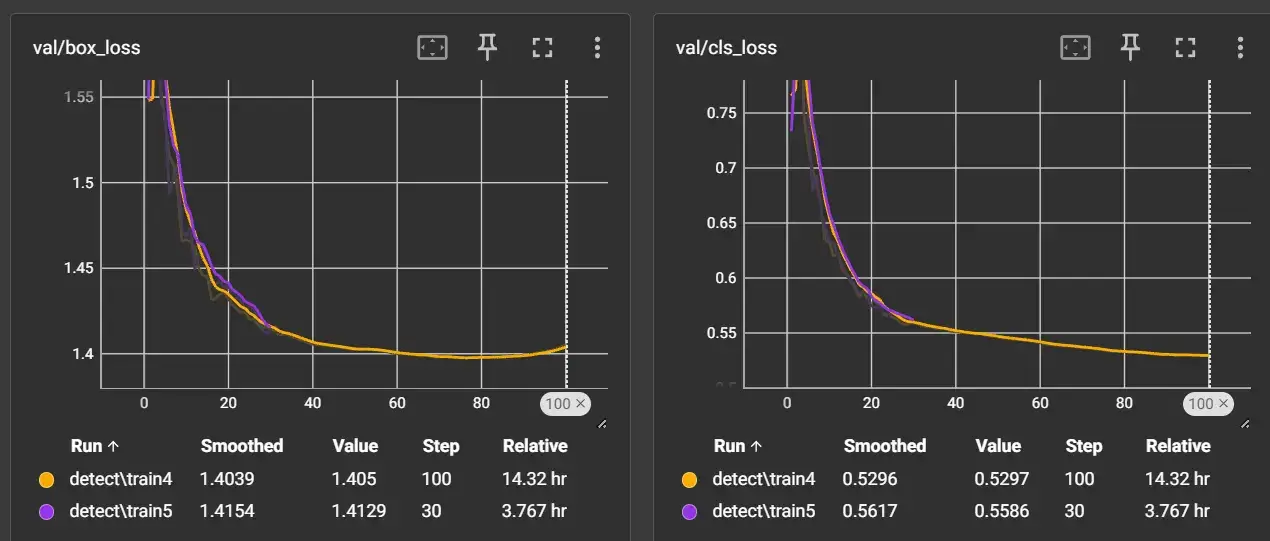
Our system offers a range of configurable options designed to meet the client’s operational needs and improve usability:
- Threshold Customization: Operators can adjust detection sensitivity to suit specific production conditions.
- Storage Management: The system provides options to change image storage paths based on operational requirements.
- Alert System and Automation: Configurable SMS alerts and real-time notifications enable immediate action when carbon soot is detected, ensuring quick response times and reducing potential quality issues.
To enhance response time, we developed a real-time alert system using a custom electronic circuit paired with a Raspberry Pi. The circuit triggers an alarm and alert light, guiding operators to the affected conveyor section for immediate action. This setup, combined with a relay connected to the Raspberry Pi, ensures seamless, high-speed communication between the AI system and the alert mechanism via fiber optic connections.
Furthermore, we integrated the client’s existing SMS alert system with our AI solution, enabling alerts to be sent directly to plant supervisors and managers. By leveraging their local server infrastructure, we streamlined the alerting process, ensuring that relevant personnel are promptly informed of any carbon soot incidents, minimizing production downtime.
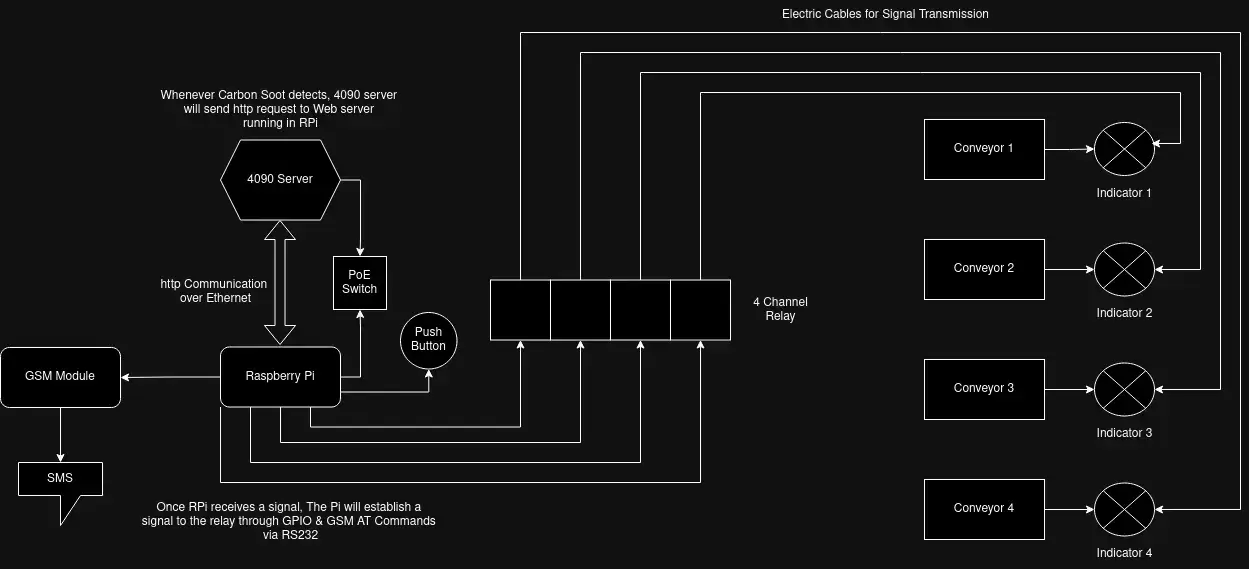
Our solution monitors four conveyor lines simultaneously, running 24/7 to meet the high-speed demands of the manufacturing environment. The client-server architecture implemented within the system ensures reliable communication, while the use of fiber optics enhances data transfer speeds and minimizes latency, further improving the overall efficiency of the detection system.
Our vision intelligence system has proven highly effective in achieving quality standards for the client, with real-time detection and automated alerts offering a proactive approach to managing carbon soot contamination. By preventing undetected particles from compromising the quality of metal components, our solution has enhanced the durability and reliability of the client’s products.
This project exemplifies the power of combining hardware innovation with AI-driven insights. As a result, our client can now maintain high-quality standards, avoid costly rework, and ensure customer satisfaction, all while benefiting from an automated and customizable solution that operates around the clock.
Our carbon soot detection system showcases Scanflow’s commitment to solving complex industrial challenges through vision intelligence. This solution, developed and deployed to handle the demanding conditions of an industrial environment, has successfully mitigated a critical production issue for our client. By leveraging AI, custom hardware, and seamless alert mechanisms, we have built a solution that is both technically robust and operationally efficient, providing our client with an advanced tool to maintain the highest quality standards in their manufacturing process.
